EnterKnow: Động cơ bốn kỳ là động cơ đốt trong sử dụng bốn hành trình pít-tông riêng biệt (nạp, nén, công suất và xả) để hoàn thành một chu kỳ hoạt động. Một Chu trình hoạt động hoàn chỉnh trong động cơ bốn kỳ cần hai vòng quay (720độ) của trục khuỷu.
Động cơ 4 kỳ là một biến thể rất phổ biến của động cơ đốt trong. Hầu hết các phương tiện chạy bằng động cơ đốt trong hiện đại đều là loại 4 kỳ, chạy bằng nhiên liệu xăng hoặc dầu diesel.
Trong quá trình hoạt động của động cơ, các piston trải qua 4 hành trình để đạt được mỗi chu kỳ công suất. Định nghĩa của một hành trình là chuyển động lên hoặc xuống của pít-tông. Sau khi hoàn thành 4 hành trình, chu kỳ sẽ hoàn tất và bắt đầu một chu kỳ mới.
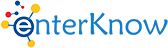
Động cơ 4 kỳ mang lại sự cân bằng tốt giữa sức mạnh, độ tin cậy và hiệu quả. Khi nói đến lượng khí thải, 4 kỳ phân tách từng sự kiện một cách cơ học, giúp giảm lượng khí thải nhiên liệu không cháy hết. Nó cũng tách dầu ra khỏi nhiên liệu, giúp giảm đáng kể lượng khí thải carbon monoxide. Sự kết hợp các đặc điểm mong muốn này đã mang lại cho động cơ 4 kỳ vị trí hàng đầu trong các phương tiện chở khách ngày nay.
Lịch sử động cơ 4 kỳ
Chu trình bốn kỳ do kỹ sư người Pháp Alphonse Beau de Rochas khởi xướng vào năm 1862. Chu trình bốn kỳ thường được gọi là chu trình Otto, theo tên kỹ sư người Đức Nikolaus August Otto, người đã thiết kế động cơ theo nguyên tắc đó vào năm 1876. Tuy nhiên, De Rochas đã có bằng sáng chế trước đó và các vụ kiện tụng tại tòa án Pháp đã ủng hộ ông.
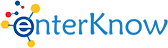
Động cơ 4 kỳ đầu tiên được trình diễn bởi Nicolaus Otto vào năm 1876. Nó tuân theo chu trình Otto và còn được gọi là động cơ chu trình Otto. Sơ đồ PV cho chu trình Otto được thể hiện, cho thấy những thay đổi mà hỗn hợp nhiên liệu – không khí trải qua về mặt thể thích và áp suât trong động cơ 4 kỳ.
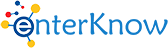
Cách thành phần của động cơ 4 kỳ
Về cơ bản, động cơ 4 kỳ bao gồm các thành phần chính: Piston, Thanh truyền, trục khuỷu, trục cam, xupap (nạp và xả), bugi (động cơ xăng), bánh đà.
Các thành phần này hoạt động với sự liên kết chặt chẽ tạo nên chu trình 4 kỳ của động cơ.

Nguyên lý làm việc của động cơ 4 kỳ
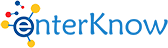
Kỳ hút – Intake Stroke: Van nạp mở, piston di chuyển từ điểm chết trên (TDC) xuống điểm chết dưới (BDC) tạo ra chân không, hút không khí hoặc hỗn hợp hòa khí (không khí + nhiên liệu) vào trong xi lanh.
Kỳ Nén – Compression Stroke: Hành trình này bắt đầu tại B.D.C, hoặc ngay khi kết thúc hành trình hút và kết thúc tại T.D.C. Trong hành trình này, pít-tông nén hỗn hợp không khí-nhiên liệu để chuẩn bị đánh lửa trong hành trình sinh công. Cả van nạp và van xả đều đóng trong giai đoạn này.
Kỳ Đốt cháy – Combustion Stroke: Còn được gọi là kỳ sinh công hay kỳ công suất. Đây là điểm bắt đầu của vòng quay thứ hai của chu kỳ bốn thì. Tại thời điểm này, trục khuỷu đã hoàn thành một vòng quay 360 độ. Trong khi piston đang ở T.D.C. (cuối kỳ nén) hỗn hợp không khí-nhiên liệu được đốt cháy bằng bugi đánh lửa (ở động cơ xăng) hoặc bằng nhiệt sinh ra khi nén cao (động cơ điêzen), đẩy pít-tông quay trở lại B.D.C. Hành trình này tạo ra công cơ học từ động cơ để làm quay trục khuỷu.
Kỳ Xả – Exhaust Stroke: Trong kỳ xả, pít-tông, một lần nữa, quay trở lại từ B.D.C. đến T.D.C. trong khi van xả đang mở. Hành động này đẩy hỗn hợp không khí-nhiên liệu đã qua sử dụng qua cổng xả.
Động cơ bốn kỳ là thiết kế động cơ đốt trong phổ biến nhất cho vận tải đường bộ có động cơ, được sử dụng trong ô tô, xe tải, tàu hỏa diesel, máy bay hạng nhẹ và xe máy. Thiết kế thay thế chính là chu trình hai thì.
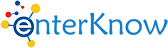
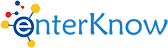
Nguyên tắc thiết kế và kỹ thuật
Giới hạn công suất đầu ra
Công suất tối đa do động cơ tạo ra được xác định bởi lượng không khí tối đa được hút vào. Lượng công suất do động cơ pít-tông tạo ra có liên quan đến kích thước của nó (thể tích xi-lanh), hiệu suất thể tích, tổn thất, tỷ lệ không khí-nhiên liệu, nhiệt trị của nhiên liệu, hàm lượng oxy trong không khí và tốc độ (RPM). Tốc độ động cơ bị giới hạn bởi độ bền vật liệu và bôi trơn. Van, pít-tông và thanh truyền chịu lực quán tính nghiêm trọng. Ở tốc độ động cơ cao, có thể xảy ra hiện tượng vỡ vật lý và rung xéc-măng pít-tông, dẫn đến tổn thất công suất hoặc thậm chí phá hủy động cơ.
Rung xéc-măng pít-tông xảy ra khi các vòng xéc-măng dao động theo chiều dọc trong các rãnh pít-tông mà chúng nằm trong đó. Rung vòng xéc-măng làm ảnh hưởng đến sự bịt kín giữa vòng xéc-măng và thành xi lanh, gây ra tổn thất áp suất và công suất xi lanh. Nếu động cơ quay quá nhanh, lò xo xu páp không thể hoạt động đủ nhanh để đóng xu páp. Hiện tượng này thường được gọi là ‘phao van’ và nó có thể dẫn đến việc pít-tông tiếp xúc với van, làm hỏng động cơ nghiêm trọng. Ở tốc độ cao, việc bôi trơn bề mặt tiếp xúc của thành xi lanh pít-tông có xu hướng bị phá vỡ. Điều này giới hạn tốc độ pít-tông đối với động cơ công nghiệp ở mức khoảng 10 m/s.
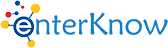
Lưu lượng cửa nạp / xả
Công suất đầu ra của động cơ phụ thuộc vào khả năng khí nạp (hỗn hợp không khí-nhiên liệu) và khí thải di chuyển nhanh chóng qua các cổng van, thường nằm ở đầu xi-lanh. Để tăng công suất đầu ra của động cơ, có thể loại bỏ các bất thường trong đường nạp và khí thải, chẳng hạn như các vết nứt đúc, và với sự trợ giúp của băng dòng không khí, bán kính của cổng van và cấu hình đế van có thể được sửa đổi để giảm lực cản. Quá trình này được gọi là porting và nó có thể được thực hiện bằng tay hoặc bằng máy CNC.
Thu hồi nhiệt thải của động cơ đốt trong
Trung bình, một động cơ đốt trong chỉ có khả năng chuyển đổi 40-45% năng lượng được cung cấp thành công cơ học. Phần lớn năng lượng thải ra ở dạng nhiệt được giải phóng ra môi trường thông qua chất làm mát, cánh tản nhiệt, v.v. Nếu bằng cách nào đó, nhiệt thải ra có thể được thu giữ và biến thành năng lượng cơ học, hiệu suất của động cơ và/hoặc hiệu suất nhiên liệu có thể được cải thiện bằng cách nâng cao hiệu quả tổng thể của chu trình. Người ta đã phát hiện ra rằng ngay cả khi 6% lượng nhiệt bị lãng phí hoàn toàn được thu hồi thì nó cũng có thể làm tăng hiệu suất của động cơ lên rất nhiều.
Nhiều phương pháp đã được nghĩ ra để tách nhiệt thải ra khỏi khí thải của động cơ và sử dụng nó để tạo ra công hữu ích, đồng thời làm giảm các chất ô nhiễm khí thải. Sử dụng Chu trình Rankine, tăng áp và tạo nhiệt điện có thể rất hữu ích như một hệ thống thu hồi nhiệt thải.
Tăng áp siêu nạp
Một cách để tăng công suất động cơ là đẩy nhiều không khí hơn vào xi lanh để có thể tạo ra nhiều công suất hơn từ mỗi hành trình công suất. Điều này có thể được thực hiện bằng cách sử dụng một số loại thiết bị nén khí được gọi là bộ siêu nạp, có thể được cung cấp năng lượng bởi trục khuỷu động cơ.
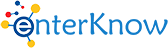
Tăng áp làm tăng giới hạn công suất đầu ra của động cơ đốt trong so với dung tích của nó. Thông thường nhất, bộ tăng áp luôn chạy, nhưng đã có những thiết kế cho phép nó bị cắt hoặc chạy ở các tốc độ khác nhau (liên quan đến tốc độ động cơ). Bộ tăng áp điều khiển bằng cơ học có nhược điểm là một phần công suất đầu ra được sử dụng để điều khiển bộ siêu nạp, trong khi năng lượng bị lãng phí trong khí thải áp suất cao, do không khí đã được nén hai lần và sau đó thu được nhiều thể tích hơn trong quá trình đốt cháy nhưng nó chỉ được giãn nở trong một giai đoạn.
Turbo tăng áp
Bộ turbo tăng áp là bộ siêu tăng áp được điều khiển bởi khí thải của động cơ, bằng tua-bin. Một bộ tăng áp được tích hợp vào hệ thống ống xả của xe để tận dụng khí thải bị thải ra. Nó bao gồm một cụm tua-bin tốc độ cao, hai mảnh với một bên nén khí nạp và bên còn lại được cung cấp năng lượng bởi luồng khí thải.
Khi chạy không tải và ở tốc độ thấp đến trung bình, tua-bin tạo ra ít năng lượng từ lượng khí thải nhỏ, bộ tăng áp ít có tác dụng và động cơ hoạt động gần như theo cách hút khí tự nhiên. Khi cần nhiều công suất hơn, tốc độ động cơ và độ mở của bướm ga sẽ tăng lên cho đến khi khí thải đủ để ‘làm nóng’ tuabin của bộ tăng áp để bắt đầu nén nhiều không khí hơn bình thường vào ống nạp.
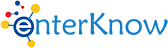
Tăng áp cho phép động cơ hoạt động hiệu quả hơn vì nó được điều khiển bởi áp suất khí thải mà nếu không sẽ bị lãng phí (hầu hết), nhưng có một giới hạn thiết kế được gọi là độ trễ tăng áp. Công suất động cơ tăng lên không có sẵn ngay lập tức do nhu cầu tăng mạnh RPM của động cơ, để tạo áp suất và quay tuabin, trước khi tuabin bắt đầu thực hiện bất kỳ hoạt động nén khí hữu ích nào. Thể tích nạp tăng lên làm tăng lượng khí thải và quay turbo nhanh hơn, v.v. cho đến khi đạt được hoạt động công suất cao ổn định. Một khó khăn khác là áp suất khí thải cao hơn khiến khí thải truyền nhiều nhiệt hơn đến các bộ phận cơ học của động cơ.
Tỷ lệ thanh truyền và hành trình piston
Tỷ lệ giữa thanh truyền và hành trình là tỷ lệ giữa chiều dài của thanh truyền với chiều dài của hành trình pít-tông. Thanh truyền dài hơn làm giảm áp suất ngang của pít-tông lên thành xi-lanh và các lực ứng suất, giúp tăng tuổi thọ động cơ. Nó cũng làm tăng chi phí và chiều cao và trọng lượng của động cơ.
“Động cơ vuông” (square engine) là động cơ có đường kính lỗ xi lanh bằng chiều dài hành trình của nó. Động cơ có đường kính lỗ xi lanh lớn hơn chiều dài hành trình của nó là động cơ oversquare engine, ngược lại, động cơ có đường kính lỗ xi lanh nhỏ hơn chiều dài hành trình là động cơ undersquare engine.
Valvetrain
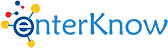
Các van thường được vận hành bởi một trục cam quay với tốc độ bằng một nửa tốc độ của trục khuỷu. Nó có một loạt các cam dọc theo chiều dài của nó, mỗi cam được thiết kế để mở một van trong phần thích hợp của hành trình nạp hoặc xả. Một chốt giữa van và cam là bề mặt tiếp xúc mà cam trượt trên đó để mở van. Nhiều động cơ sử dụng một hoặc nhiều trục cam “phía trên” một hàng (hoặc từng hàng) xi lanh, trong đó mỗi cam trực tiếp tác động một van thông qua một chốt phẳng. Trong các thiết kế động cơ khác, trục cam nằm trong cacte, trong trường hợp đó, mỗi cam thường tiếp xúc với một thanh đẩy, thanh này tiếp xúc với cần cò mổ để mở van hoặc trong trường hợp động cơ đầu phẳng thì không cần thanh đẩy. Thiết kế cam trên cao thường cho phép tốc độ động cơ cao hơn vì nó cung cấp đường dẫn trực tiếp nhất giữa cam và van. (Tham khảo: OHV, OHC, SOHC và DOHC)
Khe hở van
Khe hở van đề cập đến khoảng cách nhỏ giữa bộ nâng van và thân van để đảm bảo rằng van đóng hoàn toàn. Trên các động cơ có điều chỉnh van cơ học, khe hở quá mức sẽ gây ra tiếng ồn từ bộ truyền van. Khe hở van quá nhỏ có thể dẫn đến việc van không đóng đúng cách. Điều này dẫn đến giảm hiệu suất và có thể làm quá nhiệt các van xả. Thông thường, khe hở van phải được điều chỉnh lại sau mỗi 20.000 dặm (32.000 km).
Hầu hết các động cơ sản xuất hiện đại đều sử dụng bộ nâng thủy lực để tự động bù hao mòn cho các bộ phận của bộ truyền động van. Dầu động cơ bẩn có thể khiến bộ nâng bị hỏng.
Cân bằng năng lượng
Động cơ Otto có hiệu suất khoảng 30%; nói cách khác, 30% năng lượng do quá trình đốt cháy tạo ra được chuyển thành năng lượng quay hữu ích ở trục đầu ra của động cơ, trong khi phần còn lại bị thất thoát do nhiệt thải, ma sát và các phụ kiện động cơ. Có một số cách để phục hồi một số năng lượng bị mất do nhiệt thải. Việc sử dụng bộ tăng áp trong động cơ diesel rất hiệu quả bằng cách tăng áp suất không khí đi vào và trên thực tế, mang lại hiệu suất tăng tương tự như khi có nhiều dung tích dịch chuyển hơn. Công ty Mack Truck, nhiều thập kỷ trước, đã phát triển một hệ thống tua-bin chuyển đổi nhiệt thải thành động năng mà nó đưa trở lại bộ truyền động của động cơ. Năm 2005, BMW công bố sự phát triển của tuabin hơi nước, một hệ thống thu hồi nhiệt hai giai đoạn tương tự như hệ thống Mack giúp thu hồi 80% năng lượng trong khí thải và tăng hiệu suất của động cơ Otto lên 15%. Ngược lại, động cơ sáu kỳ có thể giảm mức tiêu thụ nhiên liệu tới 40%.
Các động cơ hiện đại thường được cố ý chế tạo để hoạt động kém hiệu quả hơn một chút so với khả năng của chúng. Điều này là cần thiết để kiểm soát khí thải chẳng hạn như tuần hoàn khí thải và bộ chuyển đổi xúc tác giúp giảm khói bụi và các chất ô nhiễm khí quyển khác. Việc giảm hiệu quả có thể được khắc phục bằng bộ điều khiển động cơ sử dụng kỹ thuật đốt cháy tinh gọn (đốt nghèo).
Tại Hoa Kỳ, Mức tiết kiệm nhiên liệu trung bình của doanh nghiệp yêu cầu các phương tiện phải đạt mức trung bình 34,9 mpg‑US (6,7 L/100 km; 41,9 mpg‑imp) so với tiêu chuẩn hiện tại là 25 mpg‑US (9,4 L/100 km; 30,0 mpg‑imp). Khi các nhà sản xuất ô tô tìm cách đáp ứng các tiêu chuẩn này vào năm 2016, các phương pháp mới để chế tạo động cơ đốt trong truyền thống (ICE) phải được xem xét. Một số giải pháp tiềm năng để tăng hiệu quả sử dụng nhiên liệu nhằm đáp ứng các nhiệm vụ mới bao gồm đốt sau khi pít-tông ở xa trục khuỷu nhất, được gọi là điểm chết trên và áp dụng chu trình Miller. Cùng với nhau, thiết kế lại này có thể giảm đáng kể mức tiêu thụ nhiên liệu và lượng khí thải NOx.